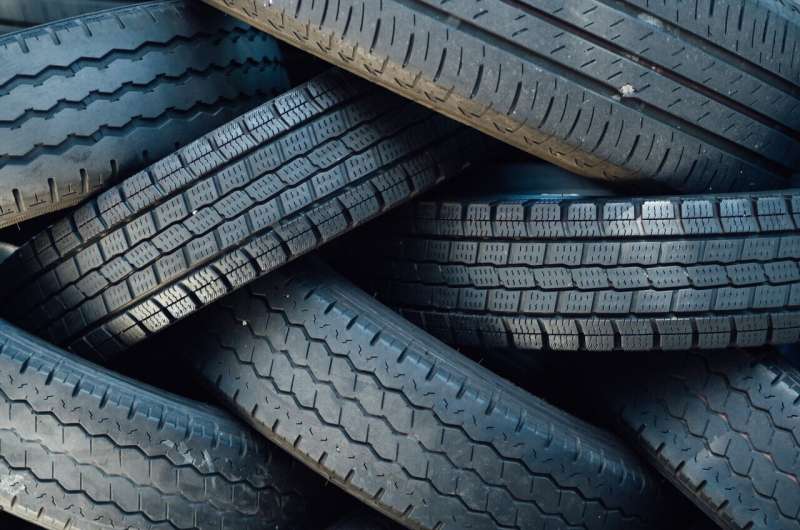
A brand new methodology to make sure consistency and high quality in rubber manufacturing, developed by a analysis crew from the College of Tennessee, Knoxville, and Eastman, is more likely to present real-world impression on materials sustainability and sturdiness for merchandise similar to automotive tires.
As shoppers within the U.S. and across the globe are more and more incentivized towards electrical autos and away from fossil-fuel reliance, present EV customers have uncovered an surprising upkeep subject. As a result of mixture of upper weight and better torque, EVs put extra strain on commonplace tires, inflicting them to degrade 30% quicker than tires on internal-combustion autos.
UT’s Fred N. Peebles Professor and IAMM Chair of Excellence Dayakar Penumadu, together with electrical engineering graduate scholar Jun-Cheng Chin, postdoctoral researcher Stephen Younger and three Eastman scientists, not too long ago printed analysis aimed toward resolving certainly one of rubber manufacturing’s most typical challenges: figuring out flaws within the materials.
Rubber incorporates components similar to zinc oxide and sulfur that work to enhance power, elasticity and different favorable traits. When the substances are usually not distributed evenly all through a rubber product similar to a automotive tire, the fabric will comprise flaws that trigger the product to degrade prematurely.
“If parts similar to sulfur don’t disperse nicely, that generates localized laborious spots,” mentioned Penumadu. “That onerous stuff attracts a variety of mechanical and thermal stresses, making the fabric degrade prematurely.”
Even a flaw the width of a human hair can lower the life span of a big rubber element similar to a automotive tire.
“That results in security and financial impacts,” Penumadu mentioned.
Figuring out and finding out such flaws—a area referred to as fracture mechanics—is important to understanding how the fabric will carry out. But discovering such flaws earlier than they trigger issues is a matter that has lengthy plagued the rubber trade.
“The present trade method is to chop out a small pattern of rubber, then observe it underneath an optical microscope,” Penumadu mentioned. “Not solely is that this tedious and damaging, it is unreliable. It requires you to guess beforehand the place, in an opaque pattern, you’ll want to verify for inconsistencies.”
As well as, optical microscopes can’t differentiate between rubber parts—for instance, sulfur and zinc oxide each seem as white specks.
Penumadu’s crew has overcome this subject by switching from optical evaluation to X-ray computed tomography. X-rays that go by the pattern are scattered and absorbed otherwise relying on the supplies they strike. A pc then reconstructs a digital 3D mannequin of the rubber’s inside.
“This can be a crucial level,” Penumadu mentioned. “XCT lets us see the within of the fabric noninvasively, and we are able to truly see the distribution of every element.”
The appliance of this new methodology will increase the rubber trade’s capability to view and predict flaws and can in the end result in extra constant high quality and longer-lasting rubber merchandise.
In October the crew acquired the 2021 Publication Excellence Award from the Journal of Rubber Chemistry and Expertise for his or her groundbreaking paper, “Sulfur Dispersion Quantitative Evaluation in Elastomeric Tire Formulations by Utilizing Excessive Decision X-Ray Computed Tomography”, which discusses the brand new XCT methodology and their analysis findings.
Dayakar Penumadu et al, SULFUR DISPERSION QUANTITATIVE ANALYSIS IN ELASTOMERIC TIRE FORMULATIONS BY USING HIGH RESOLUTION X-RAY COMPUTED TOMOGRAPHY, Rubber Chemistry and Expertise (2021). DOI: 10.5254/rct.21.79997
Quotation:
Staff develops new methodology to find out flaws in rubber (2022, October 28)
retrieved 30 October 2022
from https://phys.org/information/2022-10-team-method-flaws-rubber.html
This doc is topic to copyright. Other than any honest dealing for the aim of personal examine or analysis, no
half could also be reproduced with out the written permission. The content material is supplied for data functions solely.